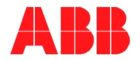
Visite du site ABB à Chassieu : dans les coulisses d’un site historique où modernisation industrielle rime avec engagement humain
02/07/2025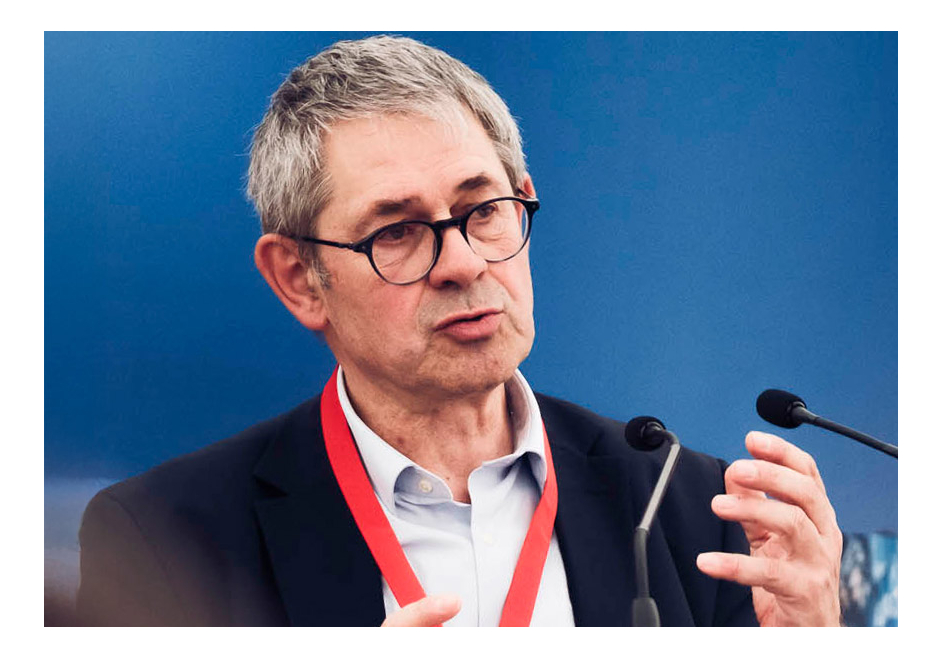
Le 5 juin dernier, à l’occasion de l’inauguration officielle de la modernisation du site de production ABB de Chassieu (Rhône), Zone Industrie a été convié à un parcours immersif dans les coulisses d’un centre d’excellence industrielle. Accompagnés par Fabien Laleuf, Directeur Général ABB France & Vice-Président Marketing & Ventes Électrification France et d’Alim Berdal, Responsable Maintenance et Production Développement, nous avons traversé une usine transformée, entre modernisation, automatisation avancée, évolution normative et maîtrise énergétique. Le parcours était ponctué de 10 étapes. Chacune d’elles fut animée par un expert de l’usine.
Fabien Laleuf, nous accueille et donne le ton, rythmé par l’engagement des équipes au travers de leurs présentations, la modernisation du process de production, la transition énergétique, la rénovation du bâtiment qui se dote d’un nouveau laboratoire R&D de 400 m² ainsi que d’une nouvelle ligne de production entièrement automatisée… vaste programme dans cette usine de contacteurs : éléments clés de l’électrification de l’industrie et de la transition énergétique. En forte croissance, ils garantissent une gestion énergétique optimisée dans la majeure partie des segments industriels, même les plus sévères, notamment les centres de données, la recharge de véhicules électriques, les énergies renouvelables et le bâtiment.
Avec cet investissement de 5 millions d’euros, ABB a misé sur une transformation structurelle du site. Ce dernier, actif depuis plus de 40 ans à Chassieu (près de Lyon), produit chaque année 4,5 millions de contacteurs – en majorité exportés à l’échelle mondiale – et fait figure de centre mondial d’excellence pour le développement et la fabrication des contacteurs dans le groupe ABB. La visite qui suit en montrera les raisons.
R&D et normalisation – La précision comme socle
Premier arrêt dans le laboratoire d’essais du site, où les équipes R&D d’ABB testent la robustesse et la longévité des contacteurs. Cette plateforme technique, certifiée ISO 17025, UL et IECEE, a bénéficié d’un investissement pour renouveler les équipements et étendre les capacités de test à de nouveaux scénarios.
Les composants sont soumis à des contraintes intensives simulant plusieurs années d’usage en environnement réel. Parmi les installations : un pont vibrant, une enceinte d’échauffement, un local d’endurance mécanique, un banc de flexion-traction, et une enceinte climatique.
« Ce laboratoire est un outil stratégique pour réduire nos délais de développement et rester à la pointe des exigences internationales », nous explique Fabien Laleuf. « Ici, les composants sont soumis à des tests thermiques, dynamiques et diélectriques simulant plusieurs années de cycles d’usage intensif en seulement quelques heures ».
HSE et performance énergétique – Une usine engagée vers la neutralité carbone
Deuxième halte de la visite : le point HSE, où la responsable détaille les actions entreprises pour améliorer l’efficacité énergétique et environnementale du site. Au-delà des équipements de production, c’est aussi l’enveloppe du bâtiment qui a été rénovée : isolation complète de la toiture, remplacement de l’ensemble des éclairages par des dispositifs LED, installation prochaine de panneaux photovoltaïques et d’une GTB (Gestion Technique du Bâtiment) pour une réduction de la consommation d’énergie.

Déjà certifié ISO 50001 pour le management de l’énergie et ISO 14001 pour la gestion environnementale, le site pilote désormais sa consommation en s’appuyant sur la plateforme numérique ABB Ability™ Energy Manager. Chaque zone, chaque ligne de production, chaque équipement est désormais monitoré en temps réel afin d’identifier les postes à forte consommation, d’optimiser les consommations et de renforcer les logiques de maintenance prédictive. « On ne se contente pas de produire mieux : on veut produire plus intelligemment, avec moins d’impact. Et pour ça, il faut une vision globale, appuyée sur des données fiables », souligne Fabien Laleuf.
Production des contacteurs AF9 – 38 Ampères– La précision industrielle à l’épreuve des cadences
Dans l’atelier dédié à la fabrication des contacteurs de taille 1 et 2 (AF9 à AF38), la visite entre dans le cœur battant de l’usine. C’est ici que sont produits chaque semaine près de 90 000 unités, grâce à l’organisation en trois équipes. Une cadence soutenue, pilotée avec une extrême rigueur sur la qualité.
Chaque contacteur est composé de deux modules distincts : une partie haute, qui contient les composants de puissance et la bobine électronique, et une partie basse, qui assure la connectique, le support et l’intégration des accessoires.
« Avec un taux de non-conformité ramené à 500 ppm, nous atteignons un niveau de qualité qui reflète l’exigence industrielle que nous nous imposons sur ce site. » précise Fabien Laleuf.
Unités de production intégrées – La polyvalence au cœur du process
Le parcours se poursuit par une présentation des Unités de Production Intégrées (UPI). Ce sont des entités autonomes rassemblant production, contrôle qualité et maintenance de premier niveau. Chacune fonctionne en flux tiré, pilotée par indicateurs de performance visuels. « L’idée est que les équipes travaillent de manière autonome et de rapprocher le geste de production du besoin client », nous explique Fabien Laleuf.

Contacteurs taille 3 & 3.5 – Puissance et contraintes mécaniques
Dans la zone dédiée aux contacteurs de taille 3 et 3.5, les volumes sont moindres que pour les gammes inférieures, mais les contraintes techniques nettement plus élevées. Chaque semaine, ce sont environ 12 000 unités qui sortent de cette ligne, destinées à des applications à haute sollicitation. « Ces contacteurs sont conçus pour encaisser des cycles intensifs dans des environnements souvent contraints : thermique, mécanique, vibrations... La stabilité de fabrication est ici non négociable » souligne Fabien Laleuf. La traçabilité produit est un élément clé chez ABB, chaque contacteur est identifié de manière unique grâce à un marquage laser précis sur le boîtier, complété par un code Datamatrix et un code-barres. Ces identifiants permettent de disposer de tout l’historique de fabrication, des composants jusqu’aux tests finaux.
La ligne « Crystal » – Vitrine technologique du site
Point d’orgue de la visite, la ligne « Crystal » incarne la nouvelle génération de production sur le site ABB de Chassieu. Dédiée à l’assemblage de la partie haute des contacteurs, elle regroupe une série d’équipements automatisés formant un ensemble cohérent et interconnecté, fruit d’une réflexion poussée sur l’optimisation des flux.
Les machines de soudure sont également entièrement automatisées au sein de cette ligne. Elles assurent les opérations de soudage des éléments critiques (bornes, connecteurs, conducteurs) avec une précision constante. L'intégration des robots ABB garantit la répétabilité des gestes et l’homogénéité des assemblages.
Deux caméras à intelligence artificielle contrôlent en continu la qualité des soudures et l’alignement des pièces, tandis que des puces RFID embarquées assurent une traçabilité sans faille tout au long de la ligne. Un convoyeur aérien relie les différentes stations et complète l'installation, assurant le transfert fluide des pièces.
« Ce nouveau dispositif d’assemblage-soudure, totalement intégré, a permis d’augmenter nos capacités de production » souligne Fabien Laleuf.
Un modèle de modernisation, entre innovation et vigilance industrielle
À l’issue de la visite, difficile de ne pas constater l’ampleur de la transformation opérée à Chassieu. L’usine conjugue automatisation, certifications, réduction énergétique et implication des équipes.
Ce projet de modernisation révèle tout le fruit du travail collectif des équipes. Leur engagement, tant dans la mise en œuvre des évolutions que dans l’accueil réservé lors de cette visite, reflète l’esprit du site de Chassieu : rigueur, maîtrise, évolution et sens du partage.